Hardware and software system promHMI
The software and hardware system PromHMI is designed to effectively organize the operational dispatch control of the substation in normal, emergency / post-emergency modes and dispatch control over the operation of equipment at the substation and adjacent electrical networks. We offer a full range of solutions and services from the supply of software and hardware for the creation of separate systems (PSCA, RPA, IATS) to the implementation of complex "turnkey" projects. The customer is given the opportunity to choose a technical solution for each specific project, depending on the characteristics of the object and its functional requirements, as well as advice on the design and implementation of the system, including on existing facilities.
Main functions of the PromHMI system:
- collection and processing of analog and discrete information about the operating mode of the substation;
- monitoring of the current mode and state of the main circuit of the substation from the dispatcher's workstation;
- automatic control and regulation (freely programmable logic in the controllers of PromHMI system);
- automated control of substation equipment;
- recording of emergency events;
- archiving and reporting;
- hardware-software operational locks;
- monitoring of the condition and operation of the main process equipment;
- automation of auxiliary technological processes;
- maintenance and synchronization of time;
- technical accounting of electric power;
- vector graphics, scaling, scrolling, automatic change in the level of detail of the circuit;
- installation on the mnemonic scheme of warning and prohibitory messages;
- monitor the status of RPA devices;
- automatic reading of oscillograms from the RPA device;
- display and processing of RPA triggering parameters (trip currents, local event viewing results);
- ensuring information and general security.
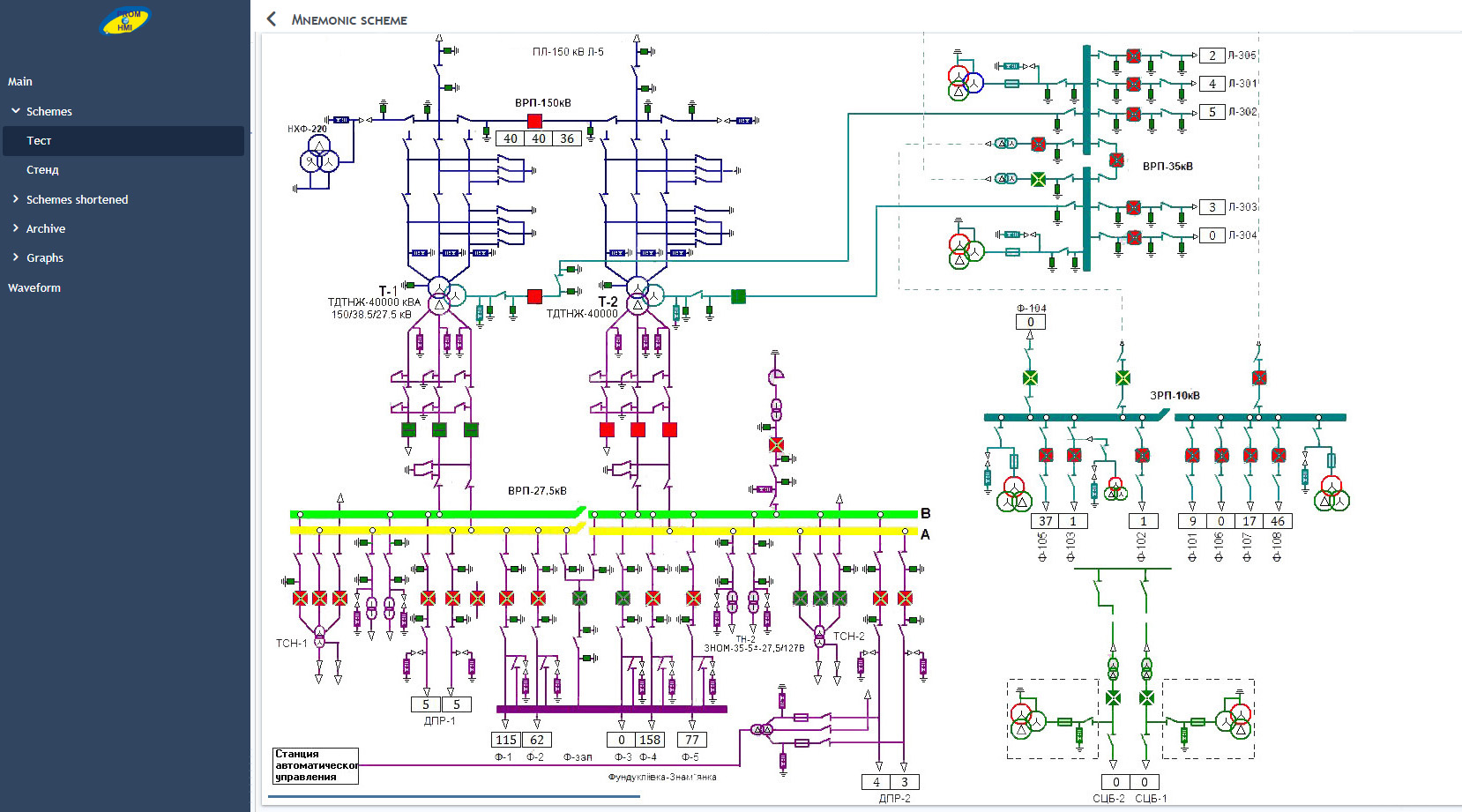
Architecture of the software and hardware system рromHMI
- The architecture of the system consists of two parts:
- 1. PromRTU controller, which directly collects data from RPA devices and other switching equipment at the substation using the existing Modbus RTU / TCP communication protocols, IEC 60870-5-101, IEC 60870-5-104, OPC and transmits data to the next level - ACS controller.
- 2. ACS controller, which takes on the fulfillment of the main tasks of the automated control system:
- conducts a survey of ACS controllers, collection, processing and storage of data;
- works with the database;
- transmits data to the upper level by various protocols (IEC 60870-5-101, IEC 60870-5-104, IEC 61850, OPC).
Main advantages of this system:
- the ability to work on a single data transfer protocol;
- no need for additional converters, adapters, media converters;
- the overlay of timestamps for the polling frequency on the transmitted data directly from the controllers;
- processing, data filtering, aperture for transferring changes directly to the dispatcher's computer, which reduces the load on the computer and reduces maintenance and upgrade costs due to no need to install a set of drivers for the final equipment of the aggregate level systems on the ACS controller;
- possibility to add a backup storage to the ACS controller. In this case, the failure of the primary server does not lead to loss of control or shutdown of the production process.
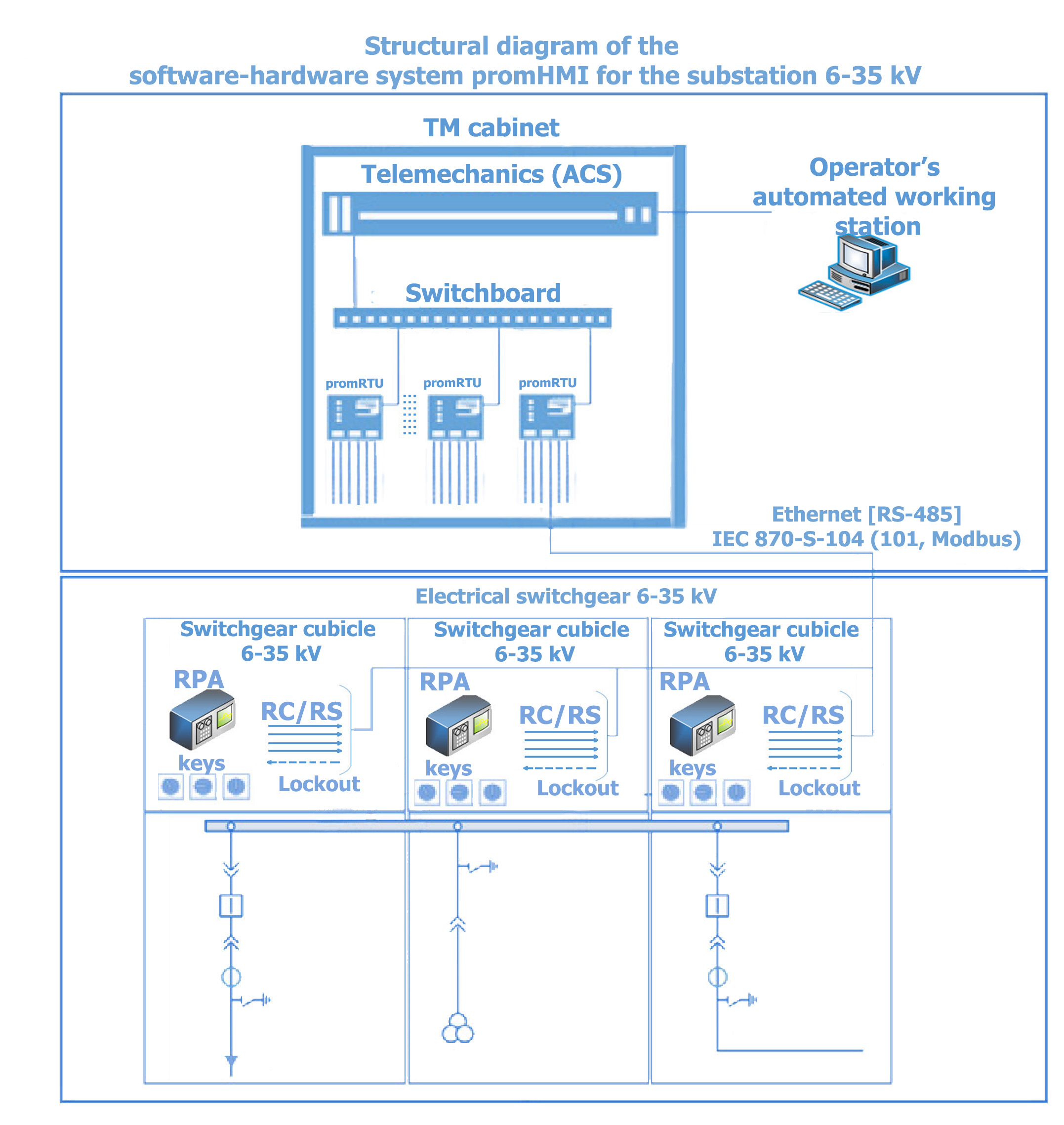
SOFTWARE OF HARDWARE SYSTEM рromSCADA
- Software of hardware system рromSCADA works under any operating system (Microsoft Windows, Linux, Mac OS).
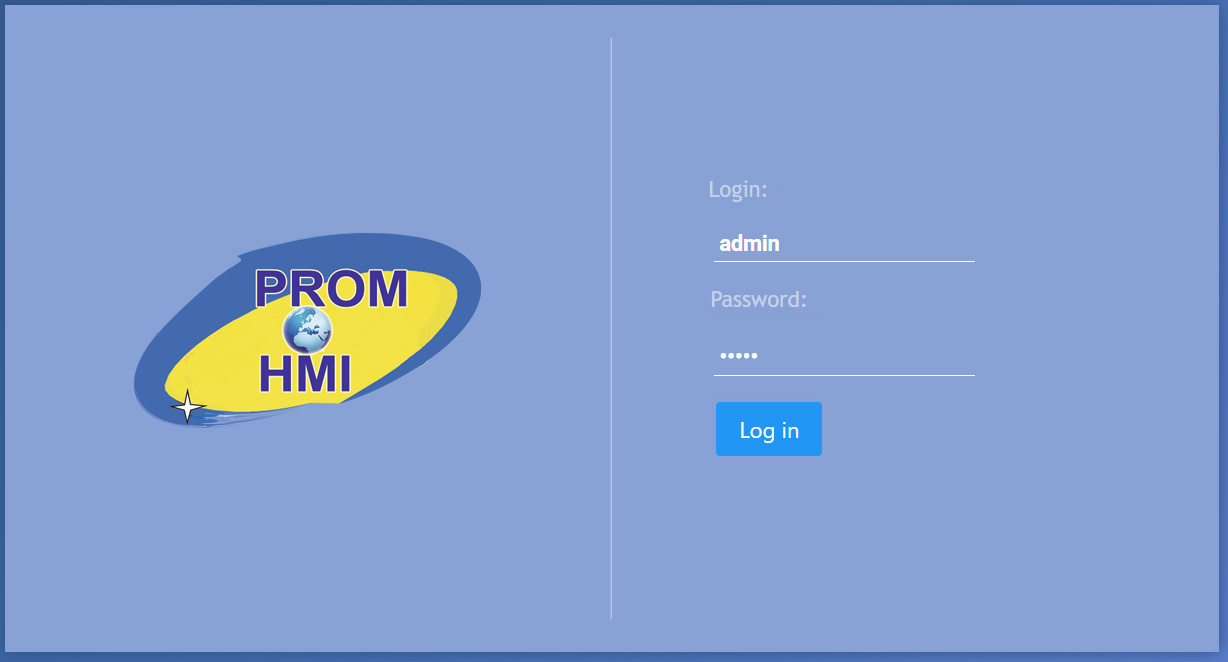
The following protocols are supported:
- IEC 60870-5-101;
- IEC 60870-5-103;
- IEC 60870-5-104;
- DNP-3;
- OPC;
- MODBUS RTU;
- MODBUS TCP;
- IEC-61850;
- IVCH.
Main functions:
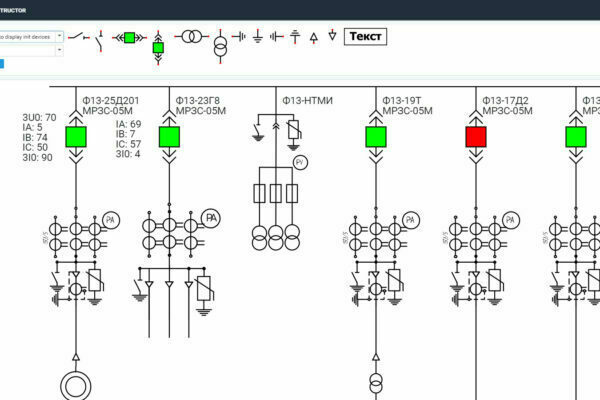
- data collection and transmission using standard communication protocols;
- storage and display of data on the operator's workstation screen;
- issuing control commands and implementing locks for specified conditions;
- processing of variable statuses technological process;
- automatic topological marking of busbars;
- support for the installation of portable grounding;
- support for manual input of TV signals;
- creation of logical calculated discrete signals based on the values of tele-signaling, using the logical functions "AND", "OR", "NOT" and their possible combinations;
- creation of logical calculation analog signals based on telemetry values using the "emergency minimum", "warning minimum", "warning maximum", "emergency maximum" and "non-update values for a period of time";
- installation on mnemonic schemes of messages by type: emergency, warning 1, warning 2, operational state;
- maintaining lists of events and alarms with flexible filtering;
- support for hierarchical structure of alarms (classes, groups, areas);
- spontaneous, cyclic archiving of data, export of archives to various systems;
- generation of reports in a .pdf file;
- backup functions support;
- administration of users and distribution of access rights.
Main advantages:
- extended event filtering mechanisms for specific objects or signals and dates with plotting;
- convenient process of creating and visualizing projects using a graphical editor - a schematic designer. Ability to create graphic symbols using ZUO graphics;
- automatic design, flexibility of re-use of templates;
- modular structure with the possibility of flexible choice of functionality enhancement;
- multi-user development environment;
- easy work with the network, use of modern network technologies;
- multi-project management;
- extensive opportunities for visualization and monitoring of processes;
- multi-window and multi-monitor technology.
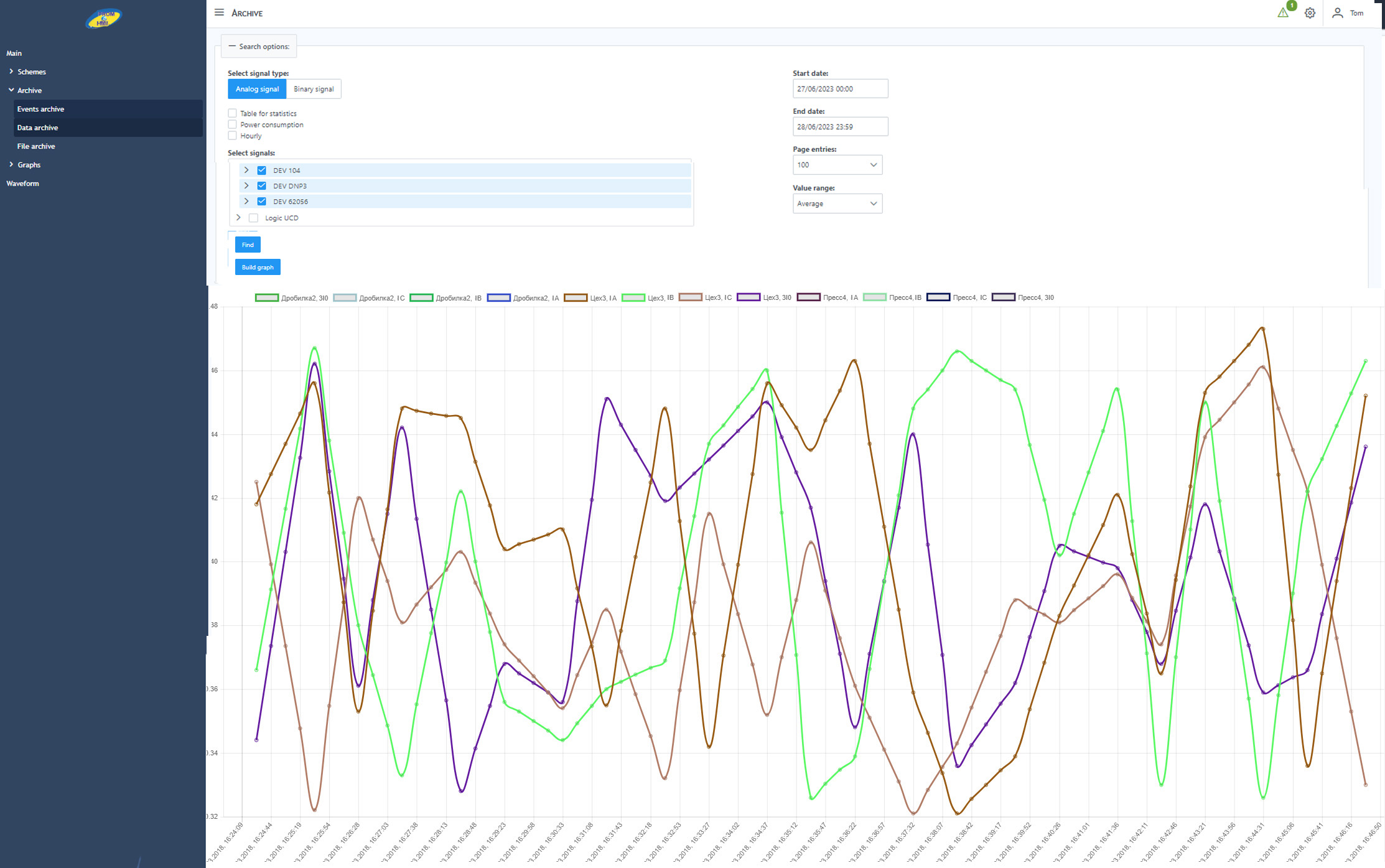
The main feature of the hardware and software system рromHMI that distinguishes it from the majority of foreign decisions and domestic developments, is that it can be shared with devices MP RPA of all domestic and foreign manufacturers, that provides support for a variety of standard communication protocols and flexible architecture of HSS. In all cases, the integration of RPA terminals is provided into APCS in its entirety, including the collection of information about start and operation, automatic reading of oscillograph recordings, control of RPA operating modes (operating input and output functions, and protection stages). Standard software from the manufacturer is used to view and change the settings.
CONTROLLERS
Compact promRTU controller PromRTU controller - the multipurpose modular product for the control and management of an electric equipment of substations, power stations and industrial enterprises. Depending on the version, the device can perform the following roles:- controller of switchgear cubicles 35-6 kV, ensuring 100% observability and controllability of cubicles;
- measuring transducer;
- field promRTU, designed to collect signals from switching devices and transformer equipment;
- build-in controller for monitoring and diagnostics of various kinds of low-voltage switch unit (cabinets of operating DC voltage system,au tomation cabinets, engineering systems of substations);
- module of input-output in the structure of classical systems of telemechanics.
Main advantages:
- The possibility of integration into industrial automation systems via the Modbus RTU / TCP protocol;
- direct control of switching devices;
- availability of different types of interfaces: RS-485 / RS-232 or Ethernet:
- compact dimensions;
- execution "without moving parts" - fanless cooling and the absence of drives on hard magnetic disks, instead of which solid state drives are used;
- buffering of data in the event of failure of communication channels with the upper level of control with subsequent transmission of the accumulated information;
- wide operating temperature range: -30 to +60 оС;
- work with standard protocols IEC 60870-5-101, IEC 60870-5-104;
- promRTU controller time synchronization is performed:
- from the SNTP/NTP server from the АСУ controller,
- according to the IEC 60870-5-104 protocol using the C_CS_NA_1 command
- long service life of the device;
- data collection from RPA devices:
- frequency of voltage for each phase;
- effective value of the voltage for each phase;
- effective value of the current for each phase;
- angle between voltage and current for each phase (power factor);
- line voltages UAB, UBC, UCA;
- active, reactive and full power for each phase;
- total capacity of the three-phase network;
- angle of three-phase load;
- voltage of zero, forward and reverse sequences U0, U1, U2;
- currents of zero, forward and reverse sequences I0, I1, I2;
- indication of operation (information exchange via ports, tele-signaling, telecontrol, voltage monitoring).
Parameter name | Value |
---|---|
Number of polling devices | Up to 30 devices per controller |
Interfaces | -RS-485 (1 or 6) -RS-232 -Ethernet (2) -4 x USB 3.0/2 x USB 2.0 |
Exchange protocols | -IEC 60870-5-101 -IEC 60870-5-104 -IEC 61850 -Modbus RTU/TCP |
Power supply | 12 V of continuous current |
Dimensions (W x H x D), mm | 187 х 111 х 50 |
Housing mounting | mounting plate VESA or 35 mm DIN rail |
Housing version | industrial |
Cooling system | passive fanless |
Compact ACS controller
- controller of telemechanics in TM systems;
- controller for the collection of general station signals from promRTU controllers as part of the automated process control systems of the substations;
- connection controller or the group of connections in the control system of the substation;
- field controller, installed outside the heated premises, intended for monitoring and controlling of switching devices and transformer equipment.
- controllers of connection (data collection from the object, control of switching devices);
- station or master controllers (polling of slave devices, communication gateway);
- controlled units (RTU - Remote Terminal Unit).
Main functions:
- data collection from promRTU controllers, primary data processing, including the verification of collected information and operational parameterization, for example, for the generation of average values of power quality indicators (PQI);
- buffering of data in the event of failure of communication channels with the upper level of control with subsequent transmission of the accumulated information;
- creation of logical calculated discrete signals based on the values of telesignaling;
- creation of logical design analog signals based on telemetry values;
- storage of data in a local archive;
- possibility of automatic information replacing from one data source with information from another data source in case of loss of communication with the first (depending on the task set by the customer);
- retransmission of data;
- maintaining a local data archive;
- diagnostics of the communication status with the lower-level devices (switching devices).
Parameter name | Value |
---|---|
Hardware platform | Interl Core i7 (4M Cache, up to 3,00 Ghz). ОЗУ 16 ГБ |
Number of connected object controllers | Not limited |
Interfaces | 2 х Ethernet (10/100/1000BASE-T) |
Operating system | Linux |
Drives | 1 x 2,5" SSD/HDD, SATA 6 Gb/sec |
Mini PCI Express | 2 slots |
USB | 4 x USB 3.0,4 x USB 2.0 |
SD Card | 1 x SD Cart Reader |
SIM | 1 slots |
Weight | 3 kg |
Power supply | 12 V of continuous current |
Dimensions (W x H x D), mm | 234 х 178 х 48 |
Housing mounting | mounting plate VESA or 35 mm DIN rail |
Cooling system | Passive fanless |